The influence of ground R6M5K5 tool steel powder in mixture with gas-atomized powder on the process properties of the powder mixtures was studied. Both powders were sifted through a 50 μm sieve. The ground powder was present in amounts of 0, 10, 20, 30, 40, 50, and 100%. The bulk density, tapped density, flowability, and repose angle of the powder mixtures were determined. Additionally, the Carr index, Hausner ratio, and flow rate were calculated. The bulk density exhibited minimal changes because of a high content of near-spherical particles in the ground powder. The flowability of the mixtures decreased with increasing content of the ground powder (flow time for the standard weighed sample increased). Grinding the powder resulted in reduction of its flowability by nearly 35%. The flowability of the gas-atomized powder was 22.49 sec/50 g. When the mixtures contained 50% ground powder, the flowability became 25.72 sec/50 g, representing a decrease of 14%. The linear fitting of the dependencies relating the bulk density (BD), flowability (τ), and flow rate (V) to the ground powder content (weight percent) in mixture with the gas-atomized powder (X) provided the following results with a high coefficient of determination (R2): BD = 4.52 – 0.0043X (R2 = 0.98), τ = 23.48 + 0.07X (R2 = 0.95), and V = 36.32 – 0.012X (R2 = = 0.97). The linear dependence of the relative bulk density (expressed in percentage) on the ground powder content demonstrated that the effect from the amount of ground powder could be assessed using the slope angle of the dependence on the abscissa axis. The slope angle of the dependence is less than 1 deg, indicating a very weak effect of the ground powder content on the relative bulk density of the powder mixtures.




Similar content being viewed by others
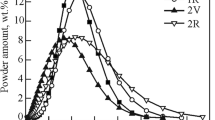
Notes
There are international ASTM B964 and Great Britain GB 1482 standards.
References
S. Vock, B. Klöden, A. Kirchner, T. Weißgärber, and B. Kieback, “Powders for powder bed fusion: a review,” Prog. Addit. Manuf., No. 4, 383–397 (2019), https://doi.org/10.1007/s40964-019-00078-6).
O.K. Radchenko, K.O. Gogaev, and V.A. Nazarenko, “Physical and process properties of fine gas-atomized R6M5K5 powders produced in different conditions,” Powder Metall. Met. Ceram., 61, No. 9–10, 489–497 (2023).
O.K. Radchenko and K.O. Gogaev, “Requirements for metal and alloy powders for 3D printing (review),” Powder Metall. Met. Ceram., 61, No. 3–4, 135–154 (2022).
K.O. Gogaev and O.K. Radchenko, Formation of Powder Systems [in Russian], Knowledge, Donetsk (2011), p. 477.
DSTU 3795–98 (ISO 4490–78, GOST 20999–98). Metallic Powders. Determination of Flowability by Means of a Calibrated Funnel (Hall Flowmeter), effective since January 1 (2000).
R.O. Grey and J.K. Beddow, “On the Hausner Ratio and its relationship to some properties of metal powders,” Powder Technol., 2, No. 6, 323–326 (1969).
L. Kanig Joseph, Lachman Leon, and A. Lieberman Herbert, The Theory and Practice of Industrial Pharmacy (3 ed.), Lea & Febiger, Philadelphia (1986), ISBN 0-8121-0977-5.
P.K. Nziu, L.M. Masu, P. Mendonidis, and A.A. Alungogo, “Characterization of titanium powder flow: A review on current status on flowability,” Mater. Sci.: Indian J., 11, Issue 7, 239–255 (2014).
J. Conceição, M. Estanqueiro, M.H. Amaral, J.P. Silva, and J.M. Sousa Lobo, “Technological excipients of tablets: Study of flow properties and compaction behavior,” Am. J. Med. Sci. Med., 2, No. 4, 71–76 (2014), https://doi.org/10.12691/ajmsm-2-4-2.
Lorenzo Marchetti and Christopher Hulme-Smith, “Flowability of steel and tool steel powders: A comparison between testing methods,” Powder Technol., 384, 402–413 (2021).
K.O. Gogaev and V.I. Ulshin, Powder Metallurgy of Tool Steels [in Russian], Knowledge, Donetsk (2012), p. 368.
Yu.F. Ternovoy (ed.), Handbook for Tool Steels [in Russian], Metallika, Kharkiv (2008), p. 224.
O.P. Vasilega, K.O. Gogaev, M.I. Grechanyuk, and V.G. Zatovskii, “Technology of producing the CoCrAlYSi alloy powder. Current issues of physical materials science,” in: Proc. Inst. Probl. Materialoved. NAN Ukrainy. Ser. Fiz. Khim. Osn. Tekhnol. Poroshk. Mater., Issue 20, 108–116 (2011).
Method and Device for Determining the Natural Angle of Repose for Loose Materials [in Ukrainian], Ukrainian Patent 86891: IPC (2009) G01B 5/24, B22F 1/00, No. f 2007 23158; appl. November 7, 2007; publ. May 25 (2009), Bulletin No. 10, p. 7.
V.Ya. Bulanov, L.I. Kvater, T.V. Dolgal, T.A. Ugolnikova, and V.B. Akimenko, Diagnostics of Metallic Powders [in Russian], Nauka, Moscow (1983), p. 229.
Author information
Authors and Affiliations
Corresponding author
Additional information
Translated from Poroshkova Metallurgiya, Vol. 62, Nos. 1–2 (549), pp. 3–12, 2023.
Rights and permissions
Springer Nature or its licensor (e.g. a society or other partner) holds exclusive rights to this article under a publishing agreement with the author(s) or other rightsholder(s); author self-archiving of the accepted manuscript version of this article is solely governed by the terms of such publishing agreement and applicable law.
About this article
Cite this article
Radchenko, O.K., Gogaev, K.O. & Nazarenko, V.A. Process Properties of Gas-Atomized and Ground Fine High-Speed Steel Powder Mixtures. Powder Metall Met Ceram 62, 1–8 (2023). https://doi.org/10.1007/s11106-023-00364-7
Received:
Published:
Issue Date:
DOI: https://doi.org/10.1007/s11106-023-00364-7