Abstract
The article presents a novel technique for performing high reduction radial shear rolling (HRRSR) of aluminum alloy bars. For this purpose, rolls with a special calibration were developed, including a high reduction section and a roll feed angle of 20°. The proposed process was investigated using FEM simulation, first. The temperature, stress-strain state, and force parameters analysis showed that the proposed method can produce defect-free bars with a natural gradient microstructure. Afterward, the experimental alloy Al-3Ca-2La-1Mn (wt%), was processed by a single-pass HRRSR process, resulting in a bar with an elongation ratio of 5. High compression and shear strains provide severe deformation of the initial cast microstructure and form a uniform distribution of small eutectic inclusions of the Al4(Ca, La) phase in the aluminum matrix. The obtained results, indicate the possibility of severe deformation of aluminum alloys using the radial shear rolling method. The proposed method of deformation can be the basis for an effective technology for obtaining bulk, long-length bars from various aluminum alloys, with a high reduction in a single pass.











Similar content being viewed by others
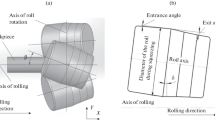
Data availability
The data presented in this study are available on request from the corresponding author.
Change history
15 January 2024
A Correction to this paper has been published: https://doi.org/10.1007/s12289-024-01810-6
References
Gamin YV, Muñoz Bolaños JA, Aleschenko AS et al (2021) Influence of the radial-shear rolling (RSR) process on the microstructure, electrical conductivity and mechanical properties of a Cu – Ni – Cr – Si alloy. Mater Sci Eng: A 822:14
Stefanik A, Szota P, Mroz S, Dyja H (2016) Application of the three-high skew rolling to magnesium rods production. Mater Test 58(5):438–441. https://doi.org/10.3139/120.110876
Iskhakov RV, Gamin YV, Kadach MV, Budnikov AS (2020) Development of radial-shear rolling mill special stands for continuous cast billets deformation. IOP Conf Ser: Mater Sci Eng 966(1):. https://doi.org/10.1088/1757-899X/966/1/012074
Arbuz A, Kawalek A, Ozhmegov K, Dyja H, Panin E et al (2020) Using of radialshear rolling to improve the structure and radiation resistance of zirconium-based alloys. Materials 13(19):. https://doi.org/10.3390/ma13194306
Potapov N, Polukhin PI (1990) Screw rolling technology. Metallurgia, Moscow in Russian
Galkin SP, Romantsev BA, Kharitonov EA (2014) Putting into practice innovative potential in the universal radialshear rolling process. CIS Iron Steel Rev 9:35–39
Galkin SP, Romantsev BA, Borowikow A (2012) New inline process for thermomechanical treatment of steel bars. CIS Iron Steel Rev 1:16–20
Galkin SP, Aleschenko AS, Romantsev BA et al (2021) Effect of preliminary deformation of continuously cast billets by radial-shear rolling on the structure and properties of hot-rolled chromium-containing steel pipes. Metallurgist. 65:185–195. https://doi.org/10.1007/s11015-021-01147-4
Sheremet’ev VA, Kudryashova AA, Dinh XT et al (2019) Advanced technology for preparing bar from medical grade Ti-Zr-Nb superelastic alloy based on combination of radial-shear rolling and rotary forging. Metallurgist 63:51–61. https://doi.org/10.1007/s11015-019-00793-z
Galkin SP, Gamin YV, Aleshchenko AS, Romantsev BA (2021) Modern development of elements of theory, technology and mini-mills of radial-shear rolling. Chernye Metally 12:51–58
Shurkin PK, Akopyan TK, Galkin SP, Aleshchenko AS (2019) Effect of radial shear rolling on the structure and mechanical properties of a new-generation high-strength aluminum alloy based on the Al – Zn – Mg – Ni – Fe system. Met Sci Heat Treat 60(11–12):764–769. https://doi.org/10.1007/s11041-019-00353-x
Kotov AD, Mochugovskiy AG, Mosleh AO, Kishchik AA, Rofman OV, Mikhaylovskaya AV (2022) Microstructure, superplasticity, and mechanical properties of Al–Mg–Er–Zr alloys. Mater Charact 186:111825. https://doi.org/10.1016/j.matchar.2022.111825
Du H, Zhang S, Zhang B et al (2021) Ca-modified Al–Mg–Sc alloy with high strength at elevated temperatures due to a hierarchical microstructure. J Mater Sci 56:16145–16157. https://doi.org/10.1007/s10853-021-06310-5
Aversa A, Marchese G, Saboori A, Bassini E, Manfredi D, Biamino S, Ugues D, Fino P, Lombardi M (2019) New aluminum alloys specifically designed for laser powder bed fusion: A review. Materials 12(7):1007. https://doi.org/10.3390/ma12071007
Belov NA, Naumova EA, Akopyan TK, Doroshenko VV (2017) Phase diagram of Al-Ca-Mg-Si system and its application for the design of aluminum alloys with high magnesium content. Metals 7(10):429. https://doi.org/10.3390/met7100429
Shurkin PK, Letyagin NV, Yakushkova AI, Ozherelkov DY, Akopyan TK (2021) Remarkable thermal stability of the Al-Ca-Ni-Mn alloy manufactured by laser-powder bed fusion. Mater Lett 285:129074. https://doi.org/10.1016/j.matlet.2020.129074
Belov N, Naumova E, Akopyan T (2017) Effect of 0.3% on microstructure, phase composition and hardening of Al-Ca-Si eutectic alloys. Trans Nonferrous Met Soc China 27(4):741–746. https://doi.org/10.1016/S1003-6326(17)60084-0
Akopyan TK, Letyagin NV, Belov NA, Koshmin AN, Gizatulin DS (2020) Analysis of the microstructure and mechanical properties of a new wrought alloy based on the ((Al) + Al4(Ca, La)) eutectic. Phys Met Metallogr 121(9):914–919. https://doi.org/10.1134/S0031918X20080025
Akopyan TK, Letyagin NV, Avxentieva NN (2020) High-tech alloys based on Al – Ca – La(–Mn) eutectic system for casting, metal forming and selective laser melting. Non-ferrous Metals 48(1):52–59. https://doi.org/10.17580/nfm.2020.01.09
Zhang S, Du H, Yao Z, Liu Z, Zhu Y, Shuai L, Huang T, Huang X, Tao X, Mondal DP, Akopyan T, Belov N (2022) Superior high temperature creep resistance of a cast Al–Mg–Ca-Sc alloy with multi-scale hierarchical microstructures. Mater Sci Eng: A 850:143533. https://doi.org/10.1016/j.msea.2022.143533
Akopyan TK, Belov NA, Naumova EA, Letyagin NV, Sviridova TA (2020) Al-matrix composite based on Al-Ca-Ni-La system additionally reinforced by L12 type nanoparticles. Trans Nonferrous Met Soc China 30(4):850–862. https://doi.org/10.1016/S1003-6326(20)65259-1
Akopyan TK, Letyagin NV, Belov NA, Shurkin PK (2019) New eutectic type Al alloys based on the Al-Ca-La(-Zr, Sc) system. Mater Today: Proc 19:2009–2012. https://doi.org/10.1016/j.matpr.2019.07.062
Akopyan TK, Letyagin NV, Sviridova TA, Korotkova NO, Prosviryakov AS (2020) New casting alloys based on the Al+Al4(Ca, La) eutectic. JOM 72(11):3779–3786. https://doi.org/10.1007/s11837-020-04340-z
Troitskii DV, Gamin YuV, Galkin SP, Budnikov AS (2023) Parametric model of a three-roll unit of radial-shear rolling mini-mill Izvestiya Vuzov. Ferrous Metall. 66(3):376–386. https://doi.org/10.17073/0368-0797-2023-3-376-386. In Russ
Valiev RZ, Islamgaliev RK, Alexandrov IV (2000) Bulk nanostructured materials from severe plastic deformation. Prog Mater Sci 45(2):103–189
Valiev RZ et al (2006) Producing bulk ultrafine-grained materials by severe plastic deformation. JOM 58(4):33–39
Kolmogorov VL (1970) Stresses, strains, fracture. Metallurgia, Moscow in Russian
Tang B, Li M, Guo N et al (2023) Genetic effects of dynamic recrystallization on ductile fracture at elevated temperature for AA7075 alloy with various stress states: modeling and simulation. Int J Mater Form 16:9. https://doi.org/10.1007/s12289-022-01730-3
Akopyan T, Gamin Y, Galkin S et al (2022) Effect of process parameters on the microstructure and mechanical properties of bars from Al-Cu-Mg alloy processed by multipass radial-shear rolling. J Mater Sci 57:8298–8313. https://doi.org/10.1007/s10853-022-07167-y
Acknowledgements
The author Ibrahim Saad ELDeeb expresses his gratitude to the Egyptian ministry of higher education and scientific research (missions’ sector) for funding his postdoctoral scholarship to produce the experimental material at National University of Science and Technology MISIS University, 4 Leninsky pr, Moscow 119049, Russia.
Funding
This work was financially supported by the Moscow Polytechnic University within the framework of the grant named after Pyotr Kapitsa.
Author information
Authors and Affiliations
Contributions
Conceptualization was contributed by Gamin Yu.V., Galkin S.P.; Methodology was contributed by Gamin Yu.V., Galkin S.P., Koshmin A.N.; Formal analysis and investigation were contributed by Mahmoud Alhaj Ali A., Nguyen X.D., ELDeeb I. S.; Writing—original draft preparation, was contributed by Mahmoud Alhaj Ali A., Nguyen X.D., ELDeeb I. S.; Writing—review and editing, was contributed by Gamin Yu.V., Mahmoud Alhaj Ali A., ELDeeb I. S.; Funding acquisition was contributed by Koshmin A.N.; Resources were contributed by Gamin Yu.V., Galkin S.P., Supervision was contributed by Gamin Yu.V., Galkin S.P.
Corresponding author
Ethics declarations
Conflict of interest
The authors have no competing interests to declare that are relevant to the content of this article.
Institutional Review Board Statement
Not applicable.
Additional information
Publisher's Note
Springer Nature remains neutral with regard to jurisdictional claims in published maps and institutional affiliations.
The original online version of this article was revised: the text indicating the numbers of the cross-sections of a workpiece, which are indicated in the figures, were incorrectly converted to citations of section headings in the article.
Rights and permissions
Springer Nature or its licensor (e.g. a society or other partner) holds exclusive rights to this article under a publishing agreement with the author(s) or other rightsholder(s); author self-archiving of the accepted manuscript version of this article is solely governed by the terms of such publishing agreement and applicable law.
About this article
Cite this article
Gamin, Y.V., Galkin, S.P., Koshmin, A.N. et al. High-reduction radial shear rolling of aluminum alloy bars using custom-calibrated rolls. Int J Mater Form 17, 5 (2024). https://doi.org/10.1007/s12289-023-01801-z
Received:
Accepted:
Published:
DOI: https://doi.org/10.1007/s12289-023-01801-z