Abstract
The design and development of Indium Tin Oxide (ITO) thin film based piezoresistive pressure sensor is presented in this paper. ITO (90:10) nanoparticles were synthesized by green combustion method using indium and tin as precursors and, carica papaya seed extract as fuel. ITO (90:10) thin film piezoresistors were deposited using synthesized nanoparticles on AlN coated circular steel (SS 304) diaphragm using E-beam evaporation technique. Diaphragm models of different thickness (0.75, 1 and 1.25 mm) were created using ANSYS finite element analysis in order to determine the maximum stress and deflection region for applied pressure of 1 to 10 bar. ANSYS results exhibited that maximum stress and deflection occurred at the center and circumference of diaphragm. ITO thin film piezoresistors were deposited at these regions using mechanical mask. TiW metal contact was established to these ITO thin film piezoresistors using DC sputtering method. ITO thin film piezoresistive pressure sensor with TiW contact connected in Wheatstone full bridge configuration was calibrated and tested for 50 pressure cycles by applying 2 V DC supply. Sensitivity (S) of the developed ITO thin film pressure sensor was obtained as 0.686, 0.566 and 0.495 mV/bar for diaphragm thickness of 0.75, 1, and 1.25 mm pressure sensors respectively. The non-linearity (NLi) in the output response of the pressure sensors was found to be 9.14, 9.82 and 11.27% for diaphragm thickness of 0.75, 1, and 1.25 mm respectively. Hysteresis errors were found to be 0.0344, 0.0525 and 0.054 for diaphragm thickness of 0.75, 1, and 1.25 mm respectively.



















Similar content being viewed by others
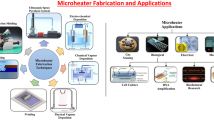
References
Fraga MA, Furlan H, Pessoa RS, Massi M (2014) Wide bandgap semiconductor thin films for piezoelectric and piezoresistive MEMS sensors applied at high temperatures: an overview. Microsyst Technol 20(1):9–21
Nguyen TK, Phan HP, Dinh T, Md Foisal AR, Nguyen NT, Dao DV (2018) High-temperature tolerance of the piezoresistive effect in p-4H-SiC for harsh environment sensing. J Mater Chem C 6(32):8613–8617
Mehregany M, Zorman CA, Rajan N, Wu CH (1998) Silicon carbide MEMS for harsh environments. Proc IEEE 86(8):1594–1609
Tougas IM, Amani M, Gregory OJ (2014) Metallic and ceramic thin film thermocouples for gas turbine engines. Sens (Switzerland) 13(11):15324–15347
Song P et al (2020) Recent progress of miniature MEMS pressure sensors. Micromachines 11(1):56
Gregory OJ, Chen X, Crisman EE (2010) Strain and temperature effects in indium-tin-oxide sensors. Thin Solid Films 518(19):5622–5625
Zhang H, Guo H, Wang Y, Zhang G, Li Z (2007) Study on a PECVD SiC-coated pressure sensor. J Micromech Microeng 17(3):426–431
Rasia LA, Mansano RD, Damiani LR, Viana CE (2010) Piezoresistive response of ITO films deposited at room temperature by magnetron sputtering. J Mater Sci 45(15):4224–4228
Latha HKE, Udayakumar A, Siddeswara Prasad V (2014) Effect of nitrogen doping on the electrical properties of 3 C-SiC thin films for high-temperature sensors applications. Acta Metall Sin (English Lett) 27(1):168–174
Phan HP, Dao DV, Nakamura K, Dimitrijev S, Nguyen NT (2015) The piezoresistive effect of SiC for MEMS sensors at high temperatures: a review. J Microelectromechanical Syst 24(6):1663–1677
Yulong Z, Libo Z, Zhuangde J (2003) A novel high temperature pressure sensor on the basis of SOI layers. Sens Actuators Phys 108:1–3
San H, Zhang H, Zhang Q, Yu Y, Chen X (2013) Silicon-glass-based single piezoresistive pressure sensors for harsh environment applications. J Micromech Microeng 23(7):075020
Bhat KN, Nayak MM (2012) Sensors- an overview of challenges in technology and packaging. Inst Smart Struct Syst J Isss 1(1):1–10
Kumar A, Yadav S, Agarwal R (2017) Design and development of a pressure transducer for high hydrostatic pressure measurements up to 200 MPa. J Inst Eng Ser C 98(4):413–420
Yang J (2013) A harsh environment wireless pressure sensing solution utilizing high temperature electronics. Sens (Switzerland) 13(3):2719–2734
Singh R, Ngo LL, Seng HS, Mok FNC (2002) A silicon piezoresistive pressure sensor. Proceedings First IEEE International Workshop on Electronic Design, Test and Applications DELTA 2002:181–184
Toriyama T, Sugiyama S (2002) Analysis of piezoresistance in n-type β-SiC for high-temperature mechanical sensors. Appl Phys Lett 81:2797–2799
Niu Z, Zhao Y, Tian B (2014)Design optimization of high pressure and high temperature piezoresistive pressure sensor for high sensitivity. Rev Sci Instrum 85(1), 015001:1–8
Fraga MA, Furlan H, Massi M, Oliveira IC, Koberstein LL (2010) Fabrication and characterization of a SiC/SiO2/Si piezoresistive pressure sensor. Procedia Eng 5(December):609–612
Jain S, Bhatia D (2017) A novel design of tactile sensor using piezoresistive cantilever for robotic application. In: Proceedings of the 2016 IEEE 7th Power India International Conference (PIICON), Bikaner, India, 25–27 November 2016; Institute of Electrical and Electronics Engineers Inc.: Piscataway
Rivera K, Gregory OJ (2018) Strain gages for SiC–SiC ceramic matrix composite engine components. IEEE Sens Lett 2:1–4
Xie H, Vitard J, Haliyo S, Ŕgnier S, Boukallel M (2008) Calibration of lateral force measurements in atomic force microscopy with a piezoresistive force sensor. Review of Scientific Instruments 79(033708):1–6
Tosolini G, Villanueva LG, Perez-Murano F, Bausells J (2012) Fast on-wafer electrical, mechanical, and electromechanical characterization of piezoresistive cantilever force sensors. Rev Sci Instrum 83(015002):1–7
Tortonese M, Barrett RC, Quate CF (1993) Atomic resolution with an atomic force microscope using piezoresistive detection. Appl Phys Lett 62:834–836
Fraga MA, Furlan H, Pessoa RS, Rasia LA, Mateus CFR (2012) Studies on SiC, DLC and TiO 2 thin films as piezoresistive sensor materials for high temperature application. Microsyst Technol 18:7–8
Eickhoff M, Möller H, Kroetz G, Berg JV, Ziermann R (1999) High temperature pressure sensor prepared by selective deposition of cubic silicon carbide on SOI substrates. Sens Actuators Phys 74(1):56–59
Wejrzanowski T, Tymicki E, Plocinski T, Bucki JJ, Tan TL (2021) Design of SiC-doped piezoresistive pressure sensor for high‐temperature applications. Sensors 21(18):1–16
Okojie RS, Lukco D, Nguyen V, Savrun E (2015) 4H-SiC piezoresistive pressure sensors at 800 ◦C with observed sensitivity recovery. IEEE Electron Device Lett 36:174–176
Toriyama T (2004) Piezoresistance consideration on n-type 6H SiC for MEMS-based piezoresistance sensors. J Micromech Microeng 14:1445–1448
George T, Son KA, Powers RA, Del Castillo LY, Okojie R (2005) Harsh environment microtechnologies for NASA and terrestrial applications. Proc IEEE Sensors vol 2005:1253–1258
Krauss AR, Auciello O, Gruen DM, Jayatissa A, Sumant A, Tucek J, Mancini DC, Moldovan N, Erdemir A, Ersoy D, Gardos MN, Busmann HG, Meyer EM, Ding MQ (2001) Ultrananocrystalline diamond thin films for MEMS and moving mechanical assembly devices. Diam Relat Mater 10:1952–1961
Wu CH, Zorman CA, Mehregany M (2006) Fabrication and testing of bulk micro machined silicon carbide piezoresistive pressure sensors for high temperature applications. IEEE Sens J 6(2):316–324
Fraga MA, Massi M, Furlan H, Oliveira IC, Rasia LA, Mateus CFR (2011) Priliminary evaluation of influence of the temperature on the performance of piezoresistive pressure sensor on a amorphous SiC thin films. Microsyst Tecghnol 17:477–480
Yang S, Zhong J, Sun B et al (2019) Influence of base pressure on property of sputtering deposited ITO film. J Mater Sci 30:13005–130012
Yadav BC, Agrahari K, Singh S et al (2016) Fabrication and characterization of nanostructured indium tin oxide film and its application as humidity and gas sensors. J Mater Sci 27:4172–4179
Lebbad A, Kerkache L, Layadi A, Leroy F, Alshehri B, Dogheche E (2018) Surface morphology, structural and electrical properties of RF-sputtered ITO thin films on si substrates. Bull Mater Sci 41(3):1–9
Mehta R, Min M, Kaul AB (2020) Sol-gel synthesized indium tin oxide as a transparent conducting oxide with solution-processed black phosphorus for its integration into solar-cells. J Vac Sci Technol B 38(6):063203
Ma Y, Zhai X, Liu J (2020) Synthesis of hexagonal-phase indium tin oxide nanoparticles by deionized water and glycerol binary solvothermal method and their resistivity. J Mater Sci 55:3860–3870
Jindal SK, Raghuwanshi SK (2015) A complete analytical model for circular diaphragm pressure sensor with freely supported edge. Microsyst Technol 21(5):1073–1079
Mala S, Latha HKE, Lalithamba HS, Udayakumar A (2022) A study on the impact of tin concentration on microstructural, dielectric and conductivity properties of ITO nanoparticles. Mater Today: Proc Vol 60:839–848
Mala S, Latha HKE, Udayakumar A, Lalithamba HS (2022) Green synthesis of ITO nanoparticles using Carica papaya seed extract: impact of annealing temperature on microstructural and electrical properties of ITO thin films for sensor applications. Mater Technol 37(10):1432–1438
Mala S, Latha HKE, Udayakumar A (2023) Influence of post–deposition annealing temperature on structural and electrical properties of TiW contact thin films. J Korean Phys Soc 83:194–199
Zeng KY, Zhu F, Hu J, Shen L, Zhang K, Gong H (2003) Investigation of mechanical properties of transparent conducting oxide thin films. Thin Solid Films 443:60
Acknowledgements
The authors thank Director and Principal of Siddaganga Institute of Technology, Tumakuru, Karnataka for the research facilities. One of the authors is thankful to the vision group of science and Technology (VGST), Govt. of Karnataka for providing funds under CISEE programme (GRD No. 645) for carrying out the research work.
Author information
Authors and Affiliations
Corresponding author
Ethics declarations
Research Involving Human Participants and/or Animals
This article does not contain any studies with human participants or animals performed by any of the authors.
Consent for Publication
Not applicable.
Competing Interest
The authors declare that they have no known competing financial interests or personal relationships that could have appeared to influence the work reported in this paper.
Additional information
Publisher’s Note
Springer Nature remains neutral with regard to jurisdictional claims in published maps and institutional affiliations.
Rights and permissions
Springer Nature or its licensor (e.g. a society or other partner) holds exclusive rights to this article under a publishing agreement with the author(s) or other rightsholder(s); author self-archiving of the accepted manuscript version of this article is solely governed by the terms of such publishing agreement and applicable law.
About this article
Cite this article
Mala, S., Latha, H.K.E. & Udayakumar, A. Design and Fabrication of Indium Tin Oxide Based Thin Film Piezoresistive Pressure Sensor. Exp Tech (2024). https://doi.org/10.1007/s40799-023-00695-5
Received:
Accepted:
Published:
DOI: https://doi.org/10.1007/s40799-023-00695-5